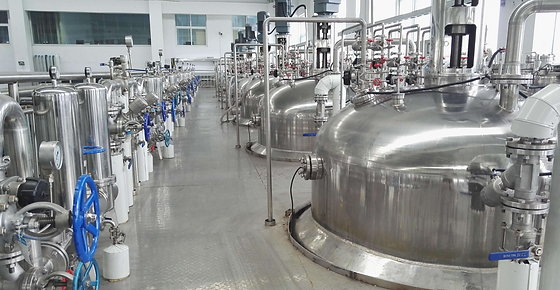
L-Lysine Production Process
Biochem
Turnkey
98.5% Pure L-Lysine :
-
Raw materials such as glucose, molasses, corn steep liquor, and salt are blended in proper ratios. The mixture is continuously sterilized and transferred to the fermentation tanks.
-
The air required for fermentation is purified through multi-stage filters and supplied using oil-free screw air compressors.
-
The fermentation strain used is Corynebacterium glutamicum, which undergoes a 45-hour cultivation process.
-
Seed preparation is carried out by culturing in flasks, followed by further cultivation in a seed tank with aeration and hydrolysate addition.
-
Fermentation takes place in specialized fermenters under controlled conditions of aeration, temperature, and pH. Sterile glucose syrup, ammonium sulfate, and antifoam agents are continuously added.
-
After fermentation, the pH is adjusted, and microbial cells are separated by microfiltration. The biomass is utilized as animal feed.
-
The L-Lysine solution undergoes decolorization with activated carbon, followed by filtration to remove the carbon.
-
Unwanted ions (such as Fe, Mg, Ca, Cl, SO3) are removed through an ion exchange system using various resins for purification.
-
The purified solution is concentrated in a vacuum evaporator and crystallizer to increase solid content.
-
Crystallized L-Lysine is separated, and the wet product is dried to meet final moisture requirements. The mother liquor is partially recycled or mixed with biomass for animal feed.
Biochem
Turnkey
68.% Pure L-Lysine :
-
Raw materials such as glucose, molasses, corn steep liquor, and salt are blended in proper ratios. The mixture is continuously sterilized and transferred to the fermentation tanks.
-
The air required for fermentation is purified through multi-stage filters and supplied using oil-free screw air compressors.
-
The fermentation strain used is Corynebacterium glutamicum, which undergoes a 45-hour cultivation process.
-
Seed preparation is carried out by culturing in flasks, followed by further cultivation in a seed tank with aeration and hydrolysate addition.
-
Fermentation takes place in specialized fermenters under controlled conditions of aeration, temperature, and pH. Sterile glucose syrup, ammonium sulfate, and antifoam agents are continuously added.
-
After fermentation, the pH is adjusted, and microbial cells are separated by microfiltration. The biomass is utilized as animal feed.
-
The L-Lysine solution undergoes decolorization with activated carbon, followed by filtration to remove the carbon.
-
Unwanted ions (such as Fe, Mg, Ca, Cl, SO3) are removed through an ion exchange system using various resins for purification.
-
The purified solution is concentrated in a vacuum evaporator and crystallizer to increase solid content.
-
Crystallized L-Lysine is separated, and the wet product is dried to meet final moisture requirements. The mother liquor is partially recycled or mixed with biomass for animal feed.
Description of Investment Components:
-
Machinery:
The machinery investment includes core equipment required for L-Lysine production from agricultural raw materials (e.g., wheat or corn). These include:
-
Wheat cleaning and steeping units
-
Wet milling systems
-
Fiber separation and germ recovery units
-
Gluten separation and starch refining systems
-
Fermentation tanks, seed culture systems
-
Evaporation, centrifugation, and drying systems
-
Storage silos, slurry handling systems
-
CIP (Cleaning-In-Place) systems
-
All related process lines and automation
Note: For 98.5% L-Lysine HCl, additional purification steps such as ion exchange, crystallization, and acidification with hydrochloric acid are included. These units are not present in the 68% purity (sulfate or liquid) L-Lysine setup, which requires simpler separation and drying processes.
-
Land & Construction:
The land and construction costs cover:
-
Industrial-zoned land
-
Production buildings
-
Administrative offices
-
Raw material & finished product warehouses
-
Laboratory units
-
Social facilities
-
Landscaping and site development
Note: Facility design for 98.5% purity plants may require additional cleanroom or controlled environment spaces due to higher product purity standards.
-
Total Investment:
Total investment includes:
-
Detailed process and mechanical engineering
-
Electrical installation and control systems
-
Infrastructure setup (roads, drainage, etc.)
-
Environmental protection units (wastewater treatment, air filtration)
-
Product handling and packaging systems
-
Licensing and compliance
-
Utility connections (electricity, water, gas)
-
Auxiliary Equipment:
Auxiliary systems not included in base machinery cost and quoted separately based on plant capacity:
-
Steam boilers
-
Cooling towers
-
Air compressors
-
Water purification (e.g., reverse osmosis systems)
-
Control panels and SCADA systems
-
Backup power generators
-
Utility monitoring and automation
-
Project Design:
Project planning and support services offered separately include:
-
Feasibility studies
-
Factory layout and 3D modeling
-
Local compliance adaptation
-
Customization based on raw material source and target market
-
Technical Service & Consulting:
-
Turnkey installation is included.
-
Remote monitoring, process optimization, and post-commissioning technical support are provided free of charge for 700 days after plant handover.
-
2008 Biochem - Turnkey, All Rights Reserved