
Efficient Centrifuge



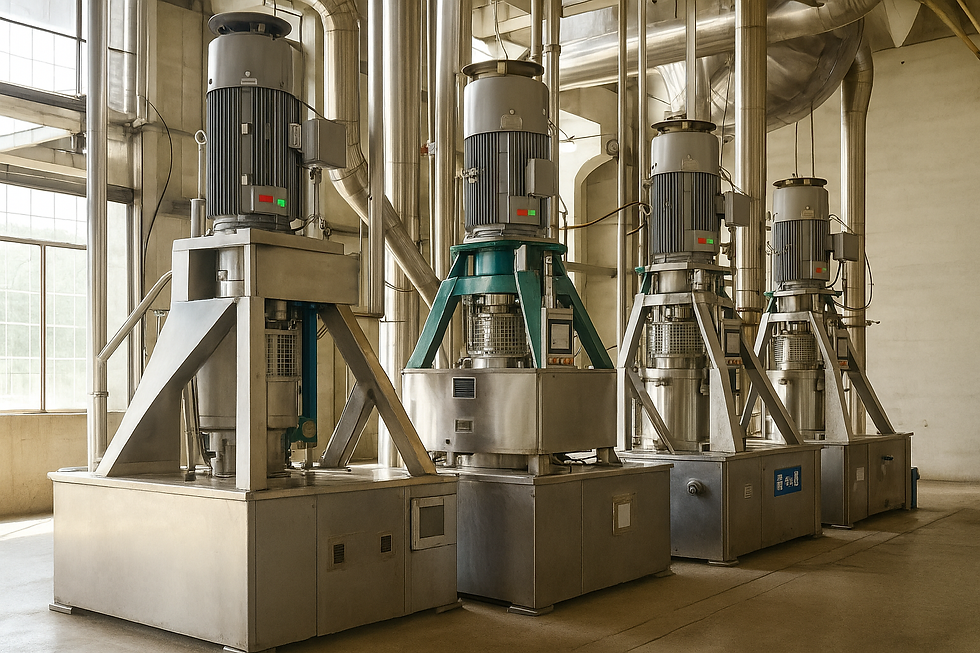

Equipment
Are you ready to take an intelligent step in your production? Our centrifuge machines deliver superior performance even in the most demanding liquid–solid and liquid–liquid phase separation processes, elevating your plant’s efficiency and product quality. With high‐speed disc stacks, you can rapidly clarify your ethanol fermentation from yeasts; and with our rugged decanter models, you can effortlessly remove protein and fiber residues from your corn and wheat starch slurries.
The AISI 316L stainless steel construction and optional Hastelloy C linings provide full protection against abrasive chemicals and high temperatures, while integrated cooling jackets preserve cell viability in your biological processes. Frequency-controlled motors ensure both energy savings and vibration-free, quiet operation. Thanks to our automatic CIP/SIP systems, cleaning and sterilization cycles are completed at the push of a button, minimizing maintenance downtime.
Optimized G-forces for each product can be easily set via intelligent control panels—simply select your desired purity level and let our system handle the rest. Whether you require high-pressure separation for sorbitol and maltodextrin production or precise particle removal for lactic acid and MSG purification, our modular design lets you flexibly configure capacity from 1 m³/h to 50 m³/h.
Ethanol
-
Centrifuge Type: Disc-stack clarifier
-
Rotor Speed & G-Force: 5,000–7,000 rpm (8,000–10,000 ×g)
-
Operating Temperature: 5–10 °C (to preserve yeast viability)
-
Flow Rate: 3–50 m³/h (single or dual-inlet models)
-
Construction Material: AISI 316L stainless steel with mirror finish
-
CIP Details:
-
8 bar cleaning at 15 min per cycle
-
Dual-circuit valves for cleaning-fluid recovery
-
-
Automation:
-
24/7 monitoring of flow, pressure, and vibration sensors
-
Parameter setup via PLC control panel
-
Corn Starch
-
Centrifuge Type: Decanter
-
Rotor Speed: ≈3,000 rpm (~3,000 ×g)
-
Solids Concentration (Dry Matter): 28–32 %
-
Flow Rate: 10–150 m³/h (modular frame design)
-
Wear Protection: Ceramic overlay on rotor interior; AISI 316L housing
-
Water Recovery: ≥ 85 % recirculation via a two-phase separation system
-
Maintenance:
-
Self-cleaning rotor design
-
Vibration monitoring for balance control
-
Citric Acid
-
Centrifuge Type: Hybrid clarifier/separator
-
G-Force: 5,000–7,000 ×g
-
Flow Rate: 5–30 m³/h
-
Temperature Control: Jacketed housing for 15–25 °C operation
-
Materials: Hastelloy C or 316L; optional internal PTFE lining for acid resistance
-
Membrane Protection: ≥ 95 % removal of solids to extend downstream membrane life
-
CIP/SIP:
-
SIP at 121 °C for 20 min
-
CIP with 6 bar alkaline/acid wash
-
Xanthan Gum
-
Centrifuge Type: Disc stack with disperser feed
-
Speed Control: 1,500–3,000 rpm (low shear to protect polymer chains)
-
Soft-Start: Minimizes mechanical stress on the product
-
Rotor Material: Carbide-reinforced AISI 316L
-
Flow Rate: 1–10 m³/h (small-scale, high-purity)
-
Surface Finish: < 0.2 µm roughness
-
Auto-Balancing: Dual sensors for real-time imbalance detection
Wheat Starch
-
Centrifuge Type: Horizontal decanter
-
G-Force: 3,500 ×g
-
Dry Matter Yield: 30–35 %
-
Flow Rate: 15–120 m³/h
-
Energy Savings: 15–20 % reduction via VFD (variable-frequency drive)
-
Rotor Design: Helical channels optimized for fiber removal
-
CIP:
-
4-step automatic cycle
-
25 % reduction in wastewater volume
-
Lysine
-
Centrifuge Type: Self-cleaning separator
-
G-Force: 9,000–12,000 ×g
-
Flow Rate: 0.5–5 m³/h (inline bioreactor feed)
-
Ultrasonic Option: Prevents solids buildup on the bowl
-
Materials: 316Ti/316L for high-temperature tolerance
-
Operating Temperature: 20–30 °C (to maintain cell viability)
-
Maintenance: Tool-free rotor removal
Sorbitol
-
Centrifuge Type: Oil-water separator disc stack
-
Max. Pressure: 10 bar
-
G-Force: 6,000 ×g
-
Flow Rate: 2–20 m³/h
-
Rotor Coating: Polypropylene for chemical resistance
-
Cooling: Integrated spiral cooling channels
-
Automation:
-
Pressure, temperature, and flow control
-
Remote monitoring via SCADA
-
Maltodextrin
-
Centrifuge Type: Clarifier with pre-filtration
-
G-Force: 4,500 ×g
-
Flow Rate: 5–25 m³/h
-
Particle Retention: ≥ 0.5 µm
-
Modular Discs: 4–12 interchangeable disc modules
-
CIP: 5 bar dual-circuit wash
Modified Starch
-
Centrifuge Type: Decanter/separator hybrid
-
G-Force: 3,000–4,000 ×g
-
Flow Rate: 10–100 m³/h
-
Water Recovery: Up to 30 % reduction in wastewater
-
Auto-Balancing: Instant shutdown on severe imbalance
-
Materials: 316L with ceramic overlay
Maltose/Dextrose Syrup
-
Centrifuge Type: Clarifier (for syrup clarification)
-
G-Force: 5,000–7,000 ×g
-
Flow Rate: 3–15 m³/h
-
Rotor Alloy: Wear-resistant titanium alloy
-
CIP: 6 bar alkaline then acid wash
-
Hygienic Design: FDA-approved seals
Lactic Acid
-
Centrifuge Type: Separator (for biomass removal)
-
G-Force: 8,000–10,000 ×g
-
Flow Rate: 1–8 m³/h
-
Sterilization: SIP capable up to 140 °C
-
Materials: Hastelloy C for maximum corrosion resistance
-
Sensors: pH and turbidity feedback control
Monosodium Glutamate
-
Centrifuge Type: Self-cleaning disc separator
-
G-Force: 7,000–9,000 ×g
-
Flow Rate: 2–12 m³/h
-
Product Purity: ≥ 99.8 % crystalline MSG
-
CIP/SIP: Fully automatic 8-stage hygiene cycle
-
Materials: 316L with PTFE-lined seals
It is also possible for us to provide customized designs tailored to your projects, our valued customer.
2008 Biochem - Turnkey, All Rights Reserved